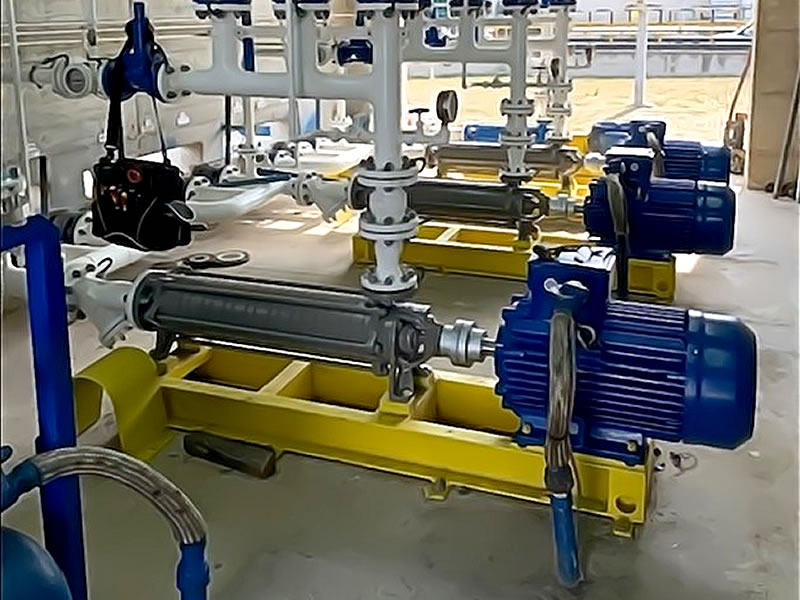
IMPROVED MAINTENANCE - REVAMPING
This plant was exhibiting corrosion and wear at an advanced stage. It was necessary to carry out amelioration and revamping which included replacement using the latest generation pumps and motors. After which the plant has returned to being efficient and competitive.
The advantages for the customer were:
- Maximum safety, environmental and related protection
- Heritage conservation
- High operational availability of the plant
- Better maintainability
- Spare parts immediately available
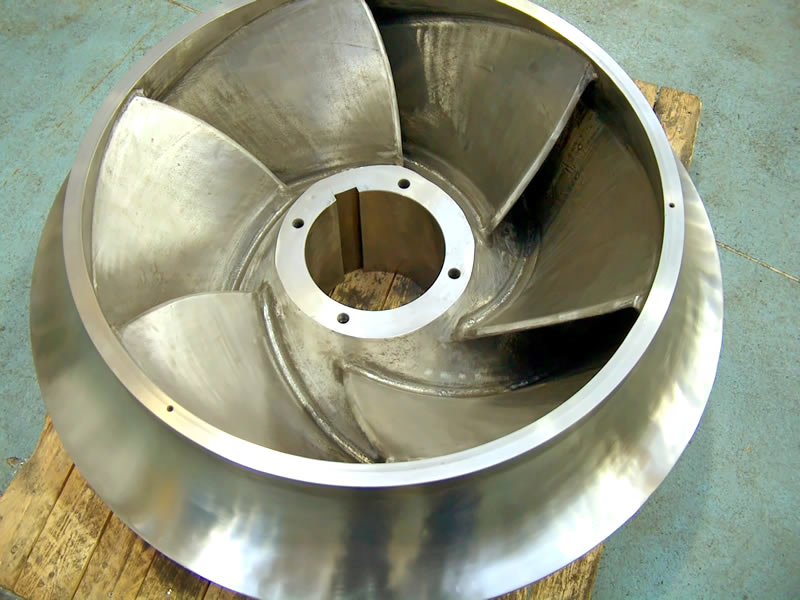
REVERSE ENGINEERING
Example of an impeller in EN JL 1040 material, rebuilt using the Reverse Engineering technique.
The advantages for the customer included:
- Detailed component analysis
- Fast turnaround
- Low price
- High quality
- Issuance of material certificates, non-destructive tests, static balancing, etc.
- Ability to improve component technology as needed
- Production of construction drawings
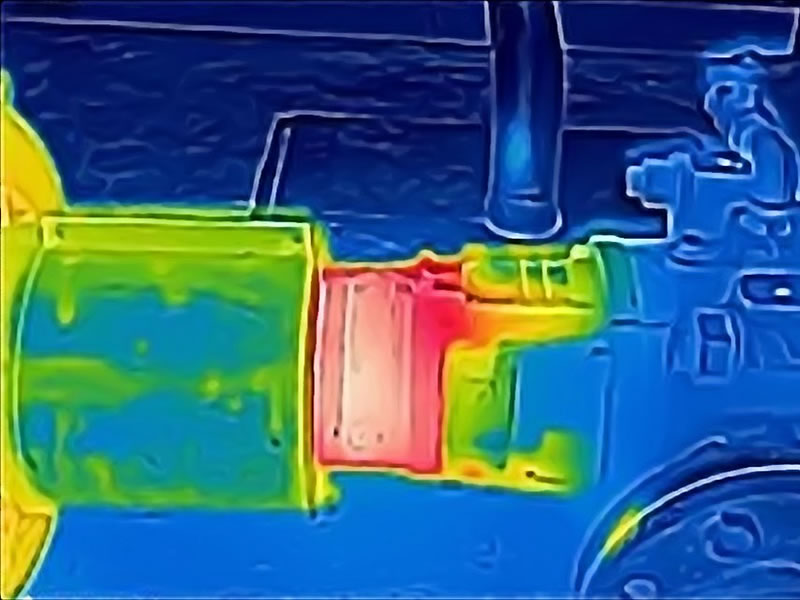
PREDICTIVE MAINTENANCE ANALYSIS OF
VIBRATIONS AND THERMOGRAPHY
Predictive Maintenance was performed with vibration analysis (with CSI 2140) and thermographic analysis (Flir E85) for a company that manages potable water. From the analysis carried out and the critical issues that emerged, it was possible to carry out a dedicated maintenance programme.
In this case, the Predictive Maintenance and Scheduled Maintenance provided helped the Customer to achieve their objectives:
- Optimization maintenance costs
- Modernization of plant
- Procurement of spare parts
- Minimize breakdowns
- Maximize process yield
- Optimize the efficiency of assets
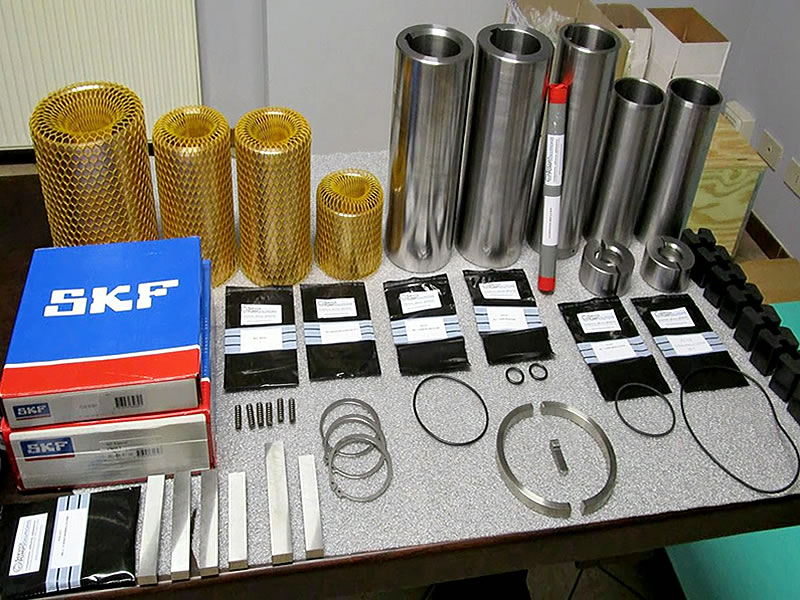
SUPPLY OF SPARE PARTS
ORIGINAL AND NON-OEM
Service Pumps Solutions can supply original spare parts, new motor / pump skids complete with base, transmission joint, cowlings and anchor bolts. We can also supply non-OEM spare parts, and through the technique of Reverse Engineering and rapid prototyping it is possible to replicate even a geometrically complex component with a swift turnaround.

FAULT MAINTENANCE
PARTIAL REVIEW PROGRAMMED ON-SITE
For a cogeneration plant that uses renewable energy to produce electricity and heat, failure maintenance was performed on the boiler feed water pumps, scheduling a partial on-site overhaul together with the customer. The partial overhaul included the replacement of the mechanical seals and bearings with original spare parts. Motor / pump axis alignment and start-up were performed. During transients and at full load, the operating parameters of the pumping group were checked, and finally the efficiency was verified by vibration analysis. Upon completion of the work, the customer was given a detailed report of the activities and the certificate of vibration analysis.
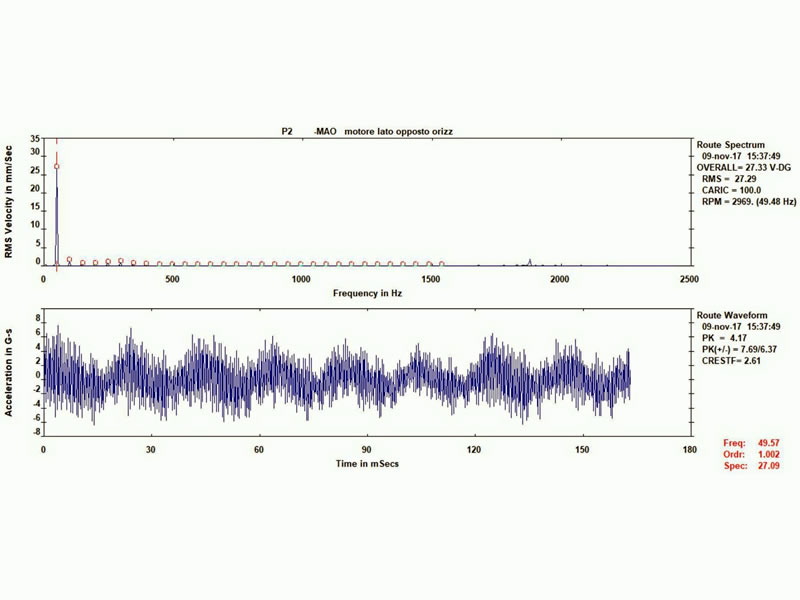
PREDICTIVE MAINTENANCE WITH CSI 2140
Where further controls of critical assets are required in production environments, Predictive Maintenance was planned with the acquisition and analysis of vibrations using the CSI 2140 tool. With this type of instrumentation Service Pumps Solutions can operate in FM, CSA Class environments. 1 div.2 Group (A, B, C, D) ATEX and IECex Zone 2, to perform data collection and vibration analysis at a higher level. Excellent results were obtained and, through the final reports, the critical issues for each machine and system were highlighted. In agreement with the Customer, it was possible to plan maintenance activities aimed at achieving the objectives set, improving: conditions of efficiency, effectiveness, operational availability, safety and process yield.
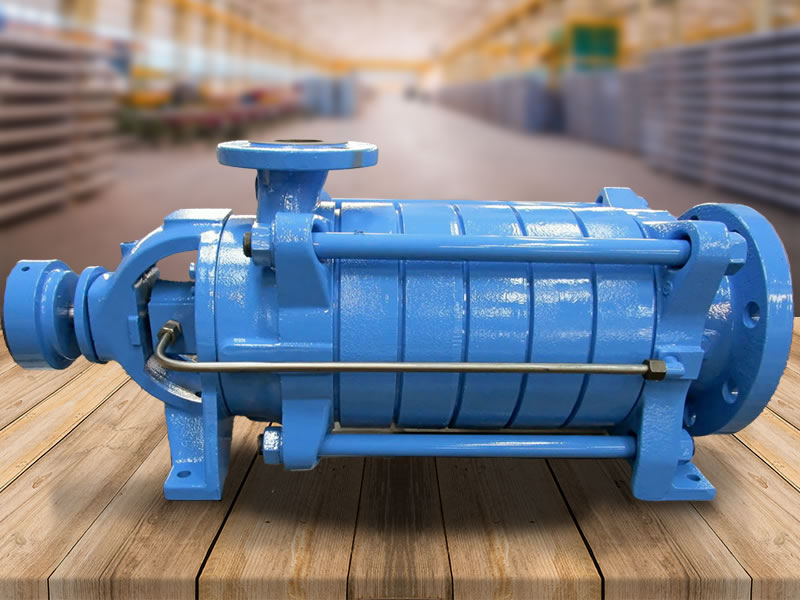
FAULT MAINTENANCE - TOTAL PUMP OVERHAUL
INSTALLATION AND START-UP
For a bottling, transfer and handling plant of liquefied petroleum gas, failure maintenance was performed, including the complete overhaul of a multistage horizontal centrifugal pump. The complete overhaul of the pump involved disassembly, cleaning, dimensional / geometric checks of all components and reassembly using original spare parts. The process was followed by a compressed air leak test and paint surface coating. Subsequently, the installation of the pump was performed on site, the motor / pump axes aligned, the flanged coupling configuration between the suction and delivery lines with the corresponding pump flanges verified. Finally, start-up was performed with the verification of the efficiency and operating parameters of the motor / pump unit.
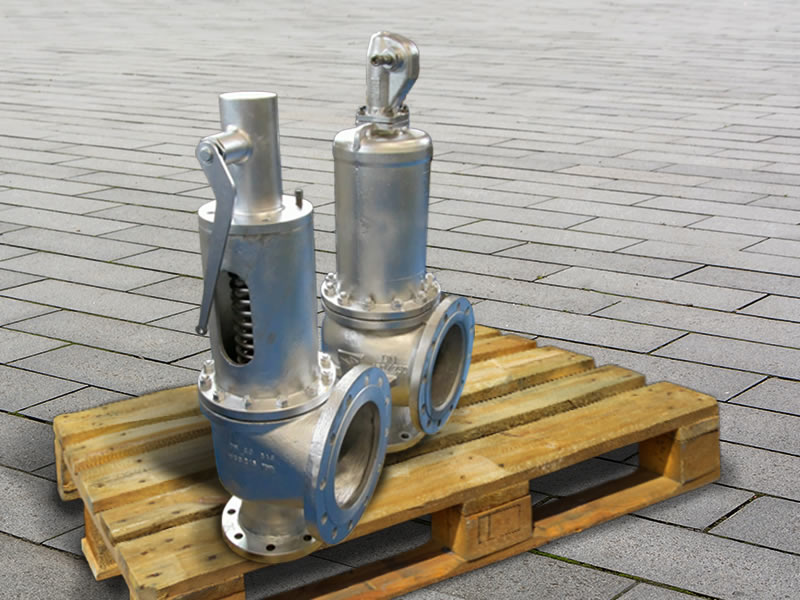
PREVENTIVE MAINTENANCE - SAFETY VALVES
For a cogeneration plant, preventive maintenance was carried out on the safety valves used on the high pressure and temperature steam lines. According to the strict regulations in force on these types of valves, it is necessary to carry out a biennial check, with mechanical service, bench calibration and test in the presence of an official from the certification body. We would like to highlight the ability of Service Pumps Solutions to operate on-site on valves that cannot be disassembled from the plant, using suitable equipment for their mechanical restoration, calibration and functional testing even with the plant in operation.

PREDICTIVE MAINTENANCE AND EFFICIENCY ANALYSIS
Predictive maintenance and efficiency checks were performed on vertical axis pump units in a river water pump station used for irrigation purposes. The main predictive inspection techniques used were thermography and vibration analysis. The thermographic analysis revealed a thermal imbalance on one phase. The fault resulted in overheating in one of the power cables and the problem was resolved by replacing the damaged cable with one of the latest generation.
The advantages for the customer were:
- Problem resolution
- Energy saving
- Optimal efficiency of the electric motor
- Return to operational safety conditions
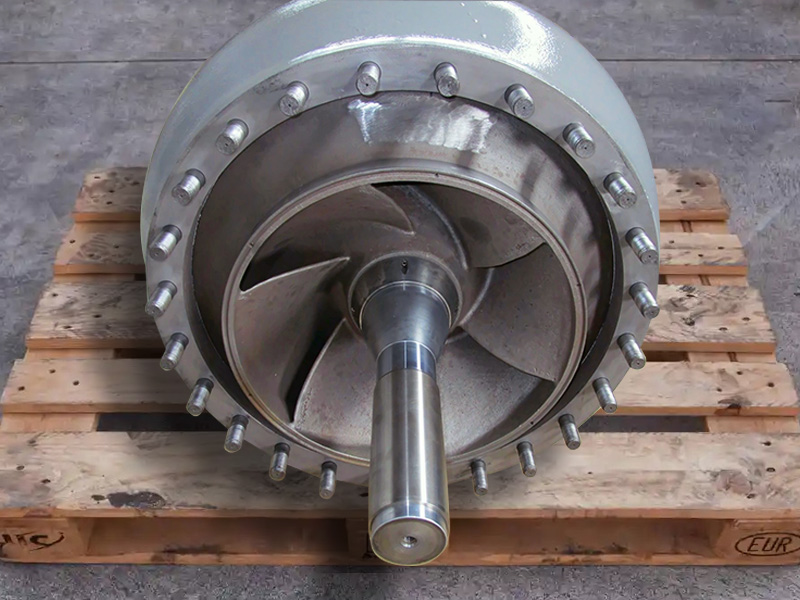
PREVENTIVE MAINTENANCE
COMPLETE OVERHAUL OF VERTICAL PUMP
The complete overhaul was carried out on a vertical axis pump for irrigation use. All the components were checked and after carrying out a detailed analysis of wear and corrosion, we proceeded with the overhaul and supply of non-OEM spare parts. Galvanic treatments were performed on some components subject to restoration to reconstruct the deteriorated surfaces and improve the efficiency of the parts. Static balancing of the impeller and subsequently dynamic balancing of the complete rotor were carried out. Finally, a partial reassembly of the pump was carried out at the workshop and concluded at the Client's premises with the installation of the complete pump. At start-up, the operating and efficiency parameters were verified.
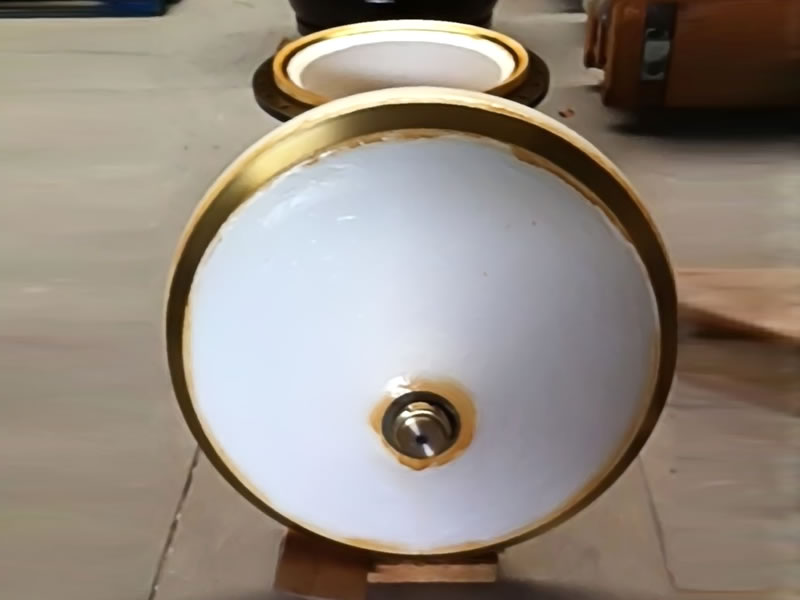
COMPLETE OVERHAUL AND STORAGE
DN700 NON-RETURN VALVE
A complete overhaul was carried out on a DN 700 Venturi non-return valve. In this instance, certain surfaces in contact with the conveyed fluid had been subject to wear. However, through multiple specialist coatings, it was possible to improve hydrophobia and reduce turbulent flow. The overhauled valve was intended for emergency use and then had to be carefully returned to conservation and storage status in the warehouse. In anticipation of the long storage period, all sensitive surfaces exposed to environmental conditions were protected with a suitable preservative product.
The advantages for the customer were:
- Improved valve efficiency
- Long-term protection against erosion and corrosion
- Coating suitable for contact with potable water
- Life extension of the component