EFFECTIVE MAINTENANCE SERVICES MADE TO MEASURE
The expertise, efficiency and reliability provided to Clients through our services makes Service Pumps Solutions a leading partner in the maintenance of pumps, valves and auxiliary systems. The aim is to accompany the Client in solving problems that can arise during the life of the machine - suggesting preventative maintenance, improvements and innovation. The implementation of innovative technological solutions is designed to maximize longevity and efficiency - ensuring optimum levels of service, operational safety and sustainability.
PUMP REPAIR FAULT MAINTENANCE

Often, strategically, the machine is brought to the point of failure. Or an unexpected fault occurs when the machine or plant is stopped. In the first case the failure is consciously expected while in the second case, major production problems can occur.
Service Pumps Solutions is ready to intervene at any time to resolve faults with pumps, valves and auxiliary systems. The initial inspection and fault analysis will be carried out; subsequently, once the corrective action has been defined together with the Client, the repair will be performed. Generally, the repair can be made on site where the machine resides. Alternatively, the work may be carried out at the Service Pumps Solutions workshop. On completion of work, a detailed technical report will be drafted on the entire procedure that was carried out.Repair procedure:
- General information / condition - recording of pump data plate
- Historical maintenance information or predictive analysis
- Disassembly, sandblasting, cleaning, visual / dimensional / geometric check of components
- List of spare parts and component refurbishment procedure
- Static balancing of components and dynamics of the rotor (if required)
- Full assembly
- Check the free movement of the rotor
- Axis alignment of drive and pump
- Start-up and efficiency check
- Final report
Advantages for the Client:
- Know who to call at any time to resolve emergency issues.
- Entrust the machine to a professional partner.
- Resolve an emergency situation, machine or plant downtime.
- Contain losses (in costs) caused by the failure.
- Return to a situation of efficiency and operational safety of the machine and / or system.
IMPROVED MAINTENANCE WHEN REPAIR IS NOT ENOUGH

A component is designed to perform a certain job, but often the operating environment and requirements change over time as a result of configuration and system changes, production, maintenance issues, corrosion and extraordinary wear. As a result, the item may no longer be suitable for carrying out its work in the intended manner, reaching failure prematurely.
Service Pumps Solutions offers a re-engineering service aimed at improving components, pumps and systems. The service offers a complete analysis of the fault and reports on the recommended technological updates, operational, maintenance or process changes.Advantages for the Client:
- Life-extension of the component, pump, valve and related systems
- Resolving safety issues and reducing the risk of future failures
- Energy saving
- Compliance with current environmental laws
- Improvement of Maintainability
- Availability of spare parts at any time (with the construction drawing available)
- Improvements in reliability, efficiency, effectiveness and operational availability
- Elimination of obsolete spare parts from the warehouse and associated reduction of cost
- Control of degradation
- Protection afforded by new component warranty
- Process sustainability
PUMP OVERHAUL PREVENTIVE MAINTENANCE
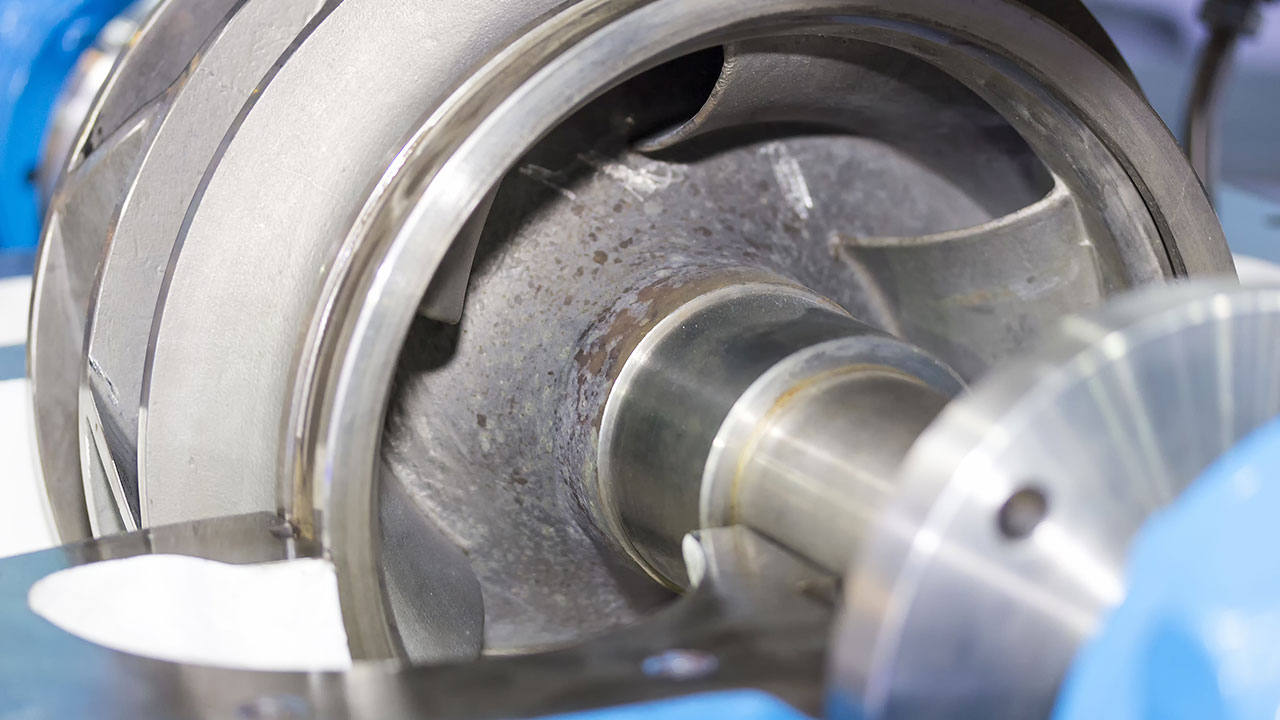
In general, for pump service and overhaul, a failure and critical analysis is first carried out to enable the definition of preventive maintenance procedures. The timing of these procedures will be programmed as close as possible to when they deemed to be necessary. According to client needs, Service Pumps Solutions offers scheduled pump maintenance services:
- Cyclical predictive maintenance is carried out according to established time intervals, or on the basis of a defined number of machines used without previous assessment of operating conditions.
- Preventive maintenance, according to condition, includes the analysis and monitoring of operating conditions, test and inspection with the aim of assigning specific maintenance to the component, system and / or machine.
- Predictive preventive maintenance is performed according to the forecast of the analysis of the reference parameters of the machines, or by evaluating their state of deterioration.
Partial overhaul activity:
- General information / condition - recording of pump data plate
- Historical maintenance information or predictive analysis
- Disassembly, cleaning, visual / dimensional control of the parts
- Standard spare parts
- Assembly of all components
- Check the free movement of the rotor
- Drive / pump axis alignment
- Start-up and efficiency check
- Final report
Complete overhaul activity:
- General information / condition - recording of pump data plate
- Historical maintenance information or predictive analysis
- Disassembly, cleaning, visual / dimensional / geometric control of the parts
- List of spare parts and component restoration activities
- Static balancing (if necessary on new parts)
- Dynamic balancing of the rotor
- Assembly of all components
- Check the free movement of the rotor, pressure test
- Application of paint finish
- Final Report
- Maintain or improve the conditions of efficiency, efficacy, operational availability, and process yield
- Reduce small stops, breakdowns, defects, start-ups, machine stoppages, efficiency loss, accidents and waste
- Degradation and wear control
- Gain operational flexibility by assessing the risks
- Extend the residual life of the component, machine, system, plant
- Raise operator professionalism (in awareness, peace of mind, motivation to exercise)
VALVE OVERHAUL AND REPAIR
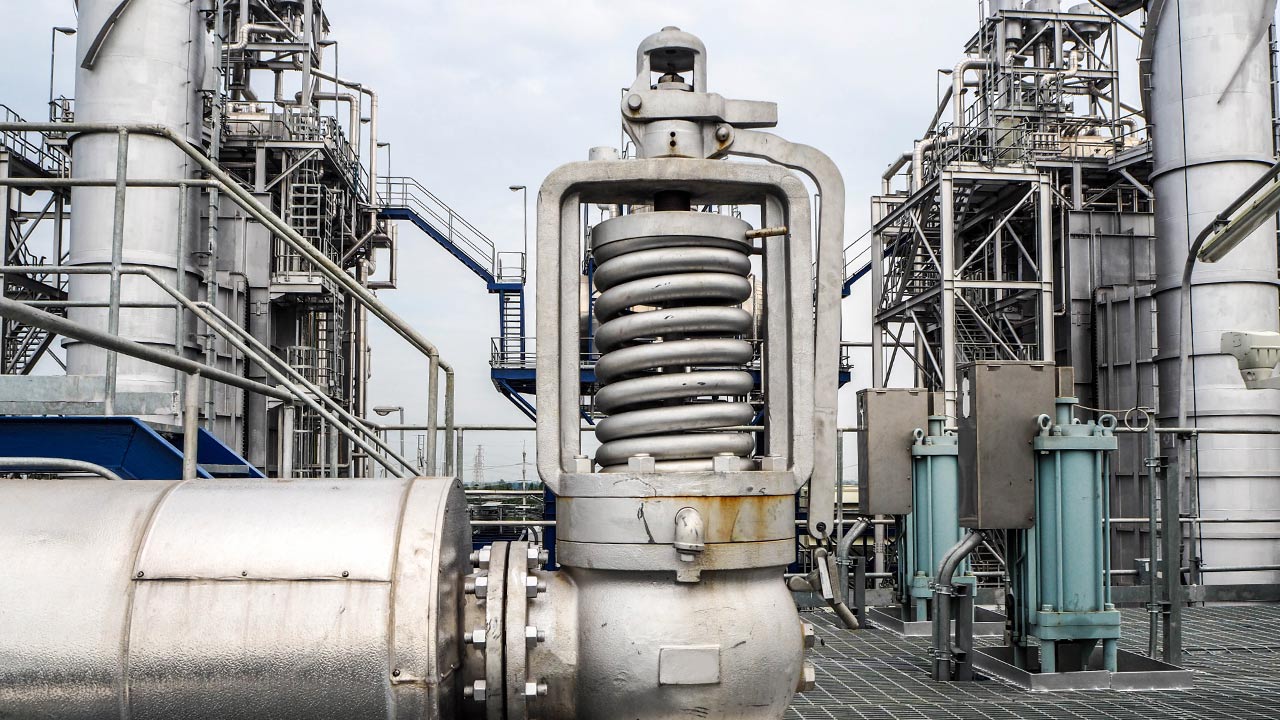
Among the primary maintenance services, Service Pumps Solutions also offers the repair or overhaul of valves of any type and construction. In many cases, the service is able to facilitate the complete restoration of efficiency and functionality of valves, even those which are very obsolete, heavily damaged or worn, and the verification of safety valves to comply with legal obligations that require, with specific intervals, efficiency and calibration control on the part of a Certifying Body.
PSV safety valve activity:- Bench, on site or in operation calibration
- Issue of the certificate of a Certifying Body
Standard Activities:
- Disassembly of all valve components
- Sandblasting and cleaning
- Dimensional/geometric component checks
- Mechanical restoration processes (turning, lapping)
- Supply of original and non-OEM spare parts including through Reverse Engineering
- Valve assembly, pressure check using water or nitrogen
- Bench calibration of valve
- Application of paint finish according to specifications
- Final report
Additional services:
- Stellite hard facing (a wear resistant alloy), substitution with Stainless steel or Inconel (corrosion resistant alloys), etc.
- Thermal treatments
- Application of various coatings, depending on use
Advantages for the Client:
- Maintain or improve conditions of efficiency, efficacy, operational availability and process yield
- Reduce small stoppages, breakdowns, defects, start-ups, efficiency losses, accidents and waste
- Degradation and wear control
- Extend the residual life of the component, valve, system, plant
- Verification and certification required by law
ROTOR REMANUFACTURE

Sometimes, after careful technical analysis and commercial evaluation, it is more convenient to regenerate an obsolete pump rotor than to replace it with a new one.
Service Pumps Solutions has extensive experience in the remanufacturing of high-tech pump rotors. The techniques adopted for the regeneration of the rotor are specific to its type, structure, use and operational environment.- Preliminary information on the pump, assessment of its use and environmental conditions
- Disassembly and cleaning of the obsolete rotor
- In-depth analysis on the surface state of the vanes
- Verification of shaft eccentricity
- Ultrasound analysis of the vanes
- Visual, dimensional and geometric check of impellers and other components
- Magnetic-particle analysis (rotor/impeller)
- Grinding of the shaft in preparation for surface coatings (chrome plating, nickel plating)
- Chrome and / or nickel plating
- Shaft finish grinding
- Static balancing of impellers and other components
- Rotor assembly, eccentricity check with free rotor and tightened bushes
- Dynamic balancing of the rotor assembly according to a specific balancing parameters
- Visual, dimensional and geometric check of impeller and other components
- Protection of the entire rotor with medium or long-term preservation treatment
- Dedicated packaging
Advantages for the Client:
- An efficient spare rotor will be available in the event of an emergency situation or scheduled total overhaul
- Reduction of pump repair and / or overhaul times
- Optimization of spare parts in stock
- Reduction of waste
- Cost reduction in case of pump repair or overhaul
STATIC AND DYNAMIC BALANCING
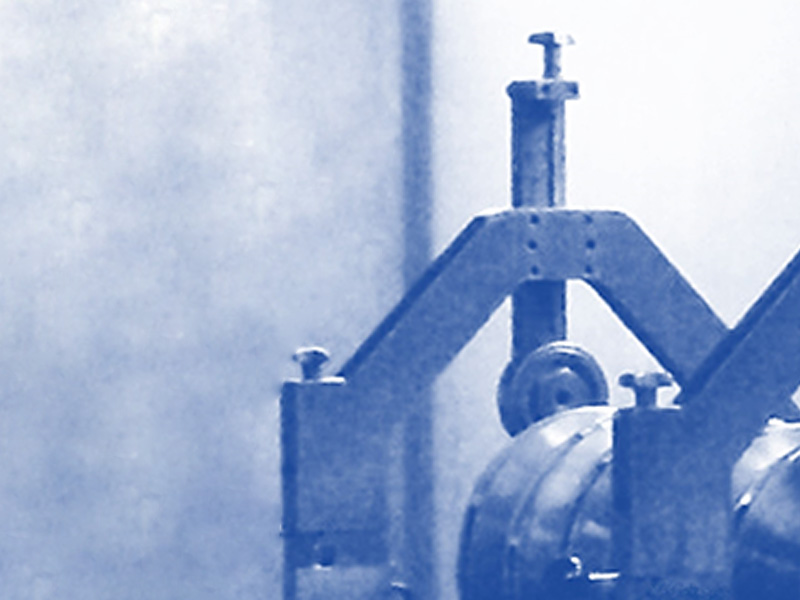
Service Pumps Solutions can provide static and dynamic balancing services on single parts and on complete rotors. Every rotating machine has a rotating element, the dynamic part subject to imbalance. Generally, a rotor consists of a shaft and the components keyed to it such as impellers, washers, bushings, discs, etc. Imbalance is understood to be the non-homogeneous distribution of mass with respect to the rotational axis. Due to the centrifugal forces of rotation, vibration and noise can be generated, amplified by any increase in the number of revolutions. In order for the pump, during service at different rotational speeds (transient or at maximum load), to present vibration within acceptable parameters, it is necessary for the rotor is balanced in advance; this process is aimed at improving the distribution of mass of the rotating bodies with respect to the axis. In each rotor there will always be a residual, but acceptable imbalance within the reference standard parameters.
Imbalance can be classified into static, coupled and dynamic. In practice, only two types are considered: static and dynamic. The appearance, function of the rotor and the type of balancing affect the position of the correction planes and the choice of the balancing tolerance.Static imbalance:
Static imbalance produces an effect under quiet conditions. Essentially, it occurs when the rotor's center of gravity is not coincident with the rotational axis. Positioned on two supports, the rotor oscillates on its own axis, moving the point of greatest mass to the lowest position due to the effect of gravity. For static balancing, generally vertical balancing machines are used and the correction is carried out on a plane.
Dynamic imbalance:
Dynamic imbalance occurs when the rotor set in rotation produces an effect. In this case the imbalances are infinitesimal, distributed along the entire rotational axis. In practice, this distribution can be grouped into two resulting imbalances which generally have different angular values and positions. To dynamically balance, horizontal balancing is used and the correction is performed on two selected planes.
For the detection in the field of dynamic rotor balancing with machines in service, Service Pumps Solutions can offer non-destructive methods employing the following techniques:- Vibration and waveform analysis
- Vibration phase analysis
- Visual inspection of components visible from the outside such as: transmission joint, balance fifth wheels, etc. (with stationary machines)
Advantages for the Client:
- Minimize the vibrations induced by the machines to within acceptable parameters
- Increased machine efficiency
- Achievement of expected component life
- Reduction or elimination of failure caused by imbalance
- Operational safety
CONDITION MONITORING

Condition monitoring is the process whereby the specific parameters of one or more machines are acquired and analyzed; facilitating advance recognition of an anomaly before it effectively becomes a fault. Anything that can be measured, acquired and transformed into mathematical language can be analyzed, controlled and improved. The most common monitoring parameters include: vibration, temperature, pressure, flow rate, voltage, current intensity, etc. Through condition monitoring techniques, with historical data and trends, Service Pumps Solutions uses predictive maintenance to determine the status of the machines and plan, together with the Client, planned maintenance and the supply of spare parts. The Condition Monitoring service offered by Service Pumps Solutions uses non-destructive techniques that are most frequently used on pumps, turbines, compressors, motors, partly completed machines, rotating and reciprocating machines in general.
Monitoring with portable analysis equipment
Monitoring with portable analysis equipment is performed by a technician who carries out measurements on specific points taken in succession (route-based) at predetermined intervals. The analysis can be carried out in real time, or later by transferring the acquired data to dedicated software. Depending on the criticality of the machines to be monitored, Service Pumps Solutions will suggest specific data acquisition rates (route-based). The Customer has the option of requesting a timely predictive analysis or, in anticipation of repeated deadlines, Service Pumps Solutions offers dedicated contract services.
Monitoring techniques offered by Service Pumps Solutions with portable analyzers:
- VIBRATION ANALYSIS
- THERMOGRAPHIC INSPECTION
- LUBRICANT ANALYSIS (tribological analysis)
- ULTRASOUND ANALYSIS (detection and analysis of compressed air leaks)
Monitoring with fixed instruments (Industry 4.0)
Generally, monitoring with fixed instruments is performed solely on critical machines within equally critical processes. In this case, monitoring is performed continuously and alarm thresholds are triggered when a parameter drifts towards the critical threshold. This monitoring system with fixed instrumentation integrates perfectly with more structured logics and Industry 4.0 systems.
Monitoring using fixed contact instruments can be carried out in two ways:
- Wired monitoring with fixed contact instruments.
The sensors are mounted directly on the machine and the sensor leads connected to the analysis system. - Wireless monitoring with fixed contact instruments using a transmitter and remote receiver.
The sensors are installed directly on the machine and, via a connected transmitter, sensor data is sent to a remote receiver over a wireless connection.
Advantages for the Client:
- Know the status of the machines
- Coping with conditions that reduce longevity before they turn into a breakdown, simultaneously avoiding the consequences
- Plan a maintenance schedule or other activities well in advance
- Elimination of sudden machine downtime and plant downtime
- Maintaining the efficiency of the machine in operational safety
- High level of plant safety
- Minimize maintenance costs
- Increase plant availability
- Concrete benefits - innovative investments - Industry 4.0 advantages
The Industry 4.0 Advantage
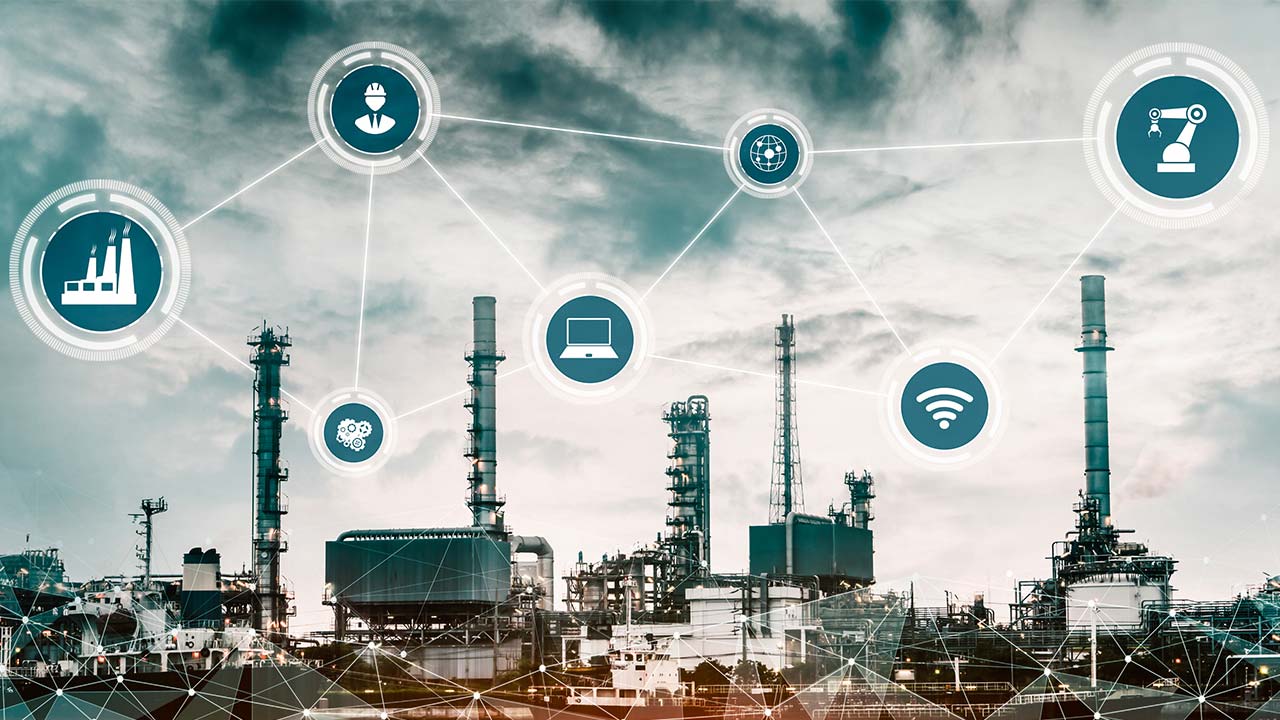
Today, with the support of Industry 4.0 and by virtue of new and increasingly sensitive digital technologies, probable anomalies can be predicted well in advance. Subsequent Scheduled Maintenance aims to improve the productivity, efficiency, reliability, competitiveness and sustainability of assets. Service Pumps Solutions can provide fixed instrumentation for data acquisition and software for checking alarm thresholds and first analysis – viewable on laptops, tablets or smartphones. Data transmission can take place remotely via cable. Fixed instrumentation is generally used for critical assets and environments.
Advantages for the Client:
- Greater production efficiency
- Reduction of idle times
- Better planning
- Improved flexibility on process control
- Reduction of waste
- Cost optimization
- Increase in revenue
- Improved professionalism, expertise, collaboration of professionals
- Greater ease of machine-operator interaction
- Smart industry
- Possible interconnectivity even with obsolete communications systems
AXIS ALIGNMENT
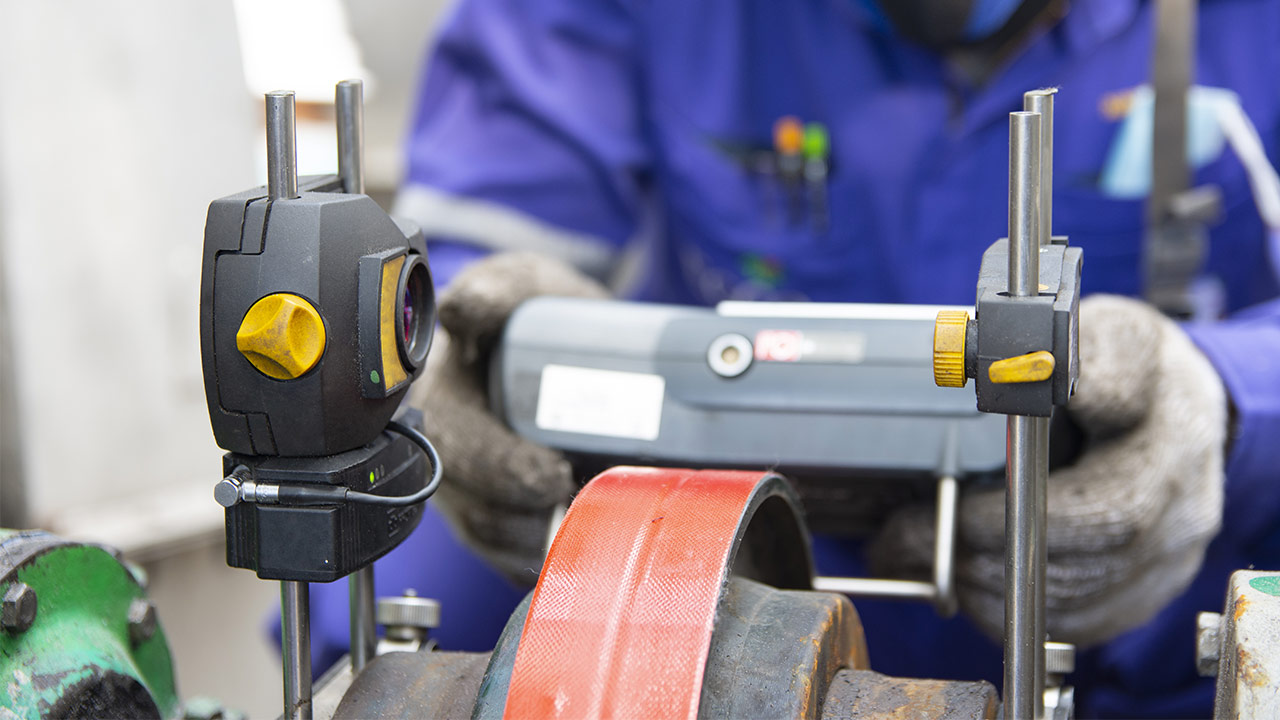
The motion is transferred from drive motor to operating component via a coupling with a transmission joint. In order for the machines to operate optimally, within permissible vibration parameters, the alignment of the axes must be guaranteed by a correct coupling of the transmission joint, performed using appropriate measurements with specific instruments.
Misalignment of the axes can originate from several points, including incorrect assembly of a joint, poor fastening, an operational displacement of the axis or due to thermal expansion.The consequences of misalignment include:
- Increase in vibration amplitude
- Reduction of component life (bearings, joints, lubricants, etc.)
- Increased risk of breakage
- Risk to operators
- Economic losses due to production downtime and emergency maintenance
According to the operating conditions of the machines and the type of transmission joint, Service Pumps Solutions adopts the following axis alignment techniques:
- Straight edge and feeler gauge - accuracy ≥ 0.1 mm
- Dial gauge - accuracy ≥ 0.01 mm
- Laser - accuracy ≥ 0.001 mm
Before each alignment, the soft foot condition is checked and, if present, corrected. In addition, for detection in the field of axis alignment with machines in service, Service Pumps Solutions can offer non-destructive methods using the following techniques:
- Vibration and waveform analysis
- Vibration phase analysis
- Infrared thermography
- Strobe lamp
- Visual inspection
REVAMPING
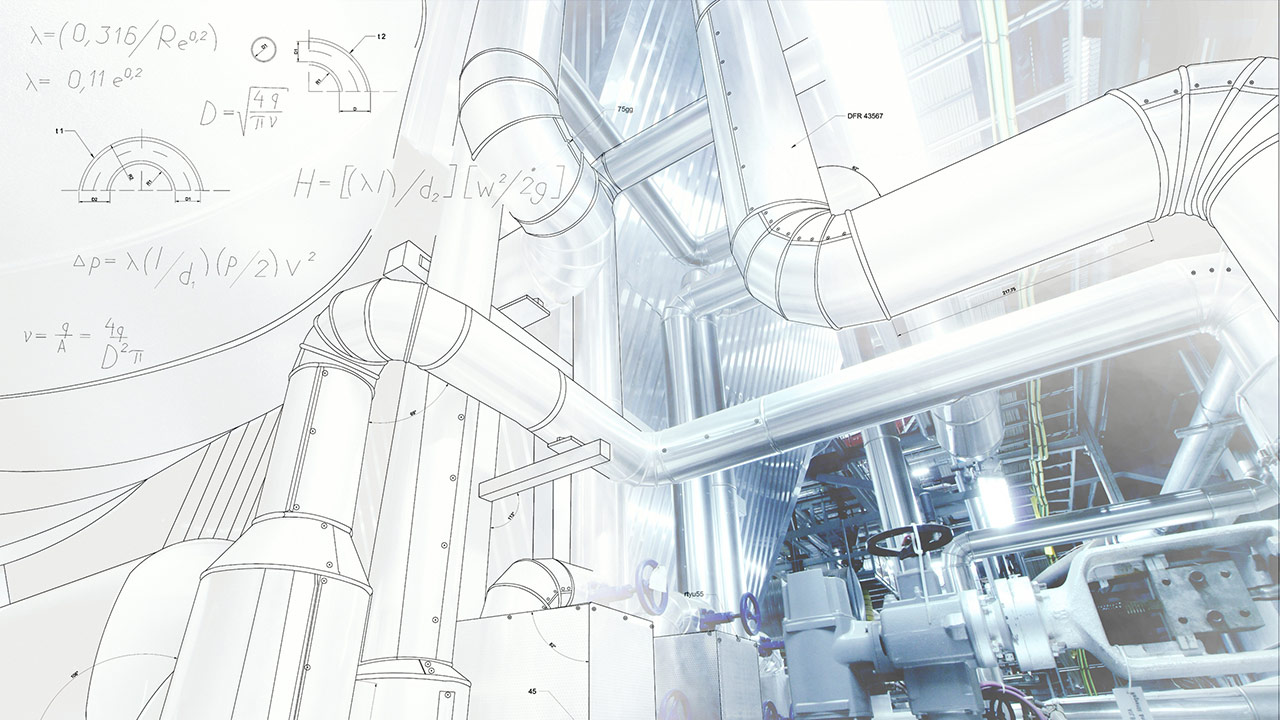
With the Revamping technique, Service Pumps Solutions offers the option of modernizing and making obsolete pump units and plant economically viable for customers who intend to maintain existing systems.
RETROFITTING
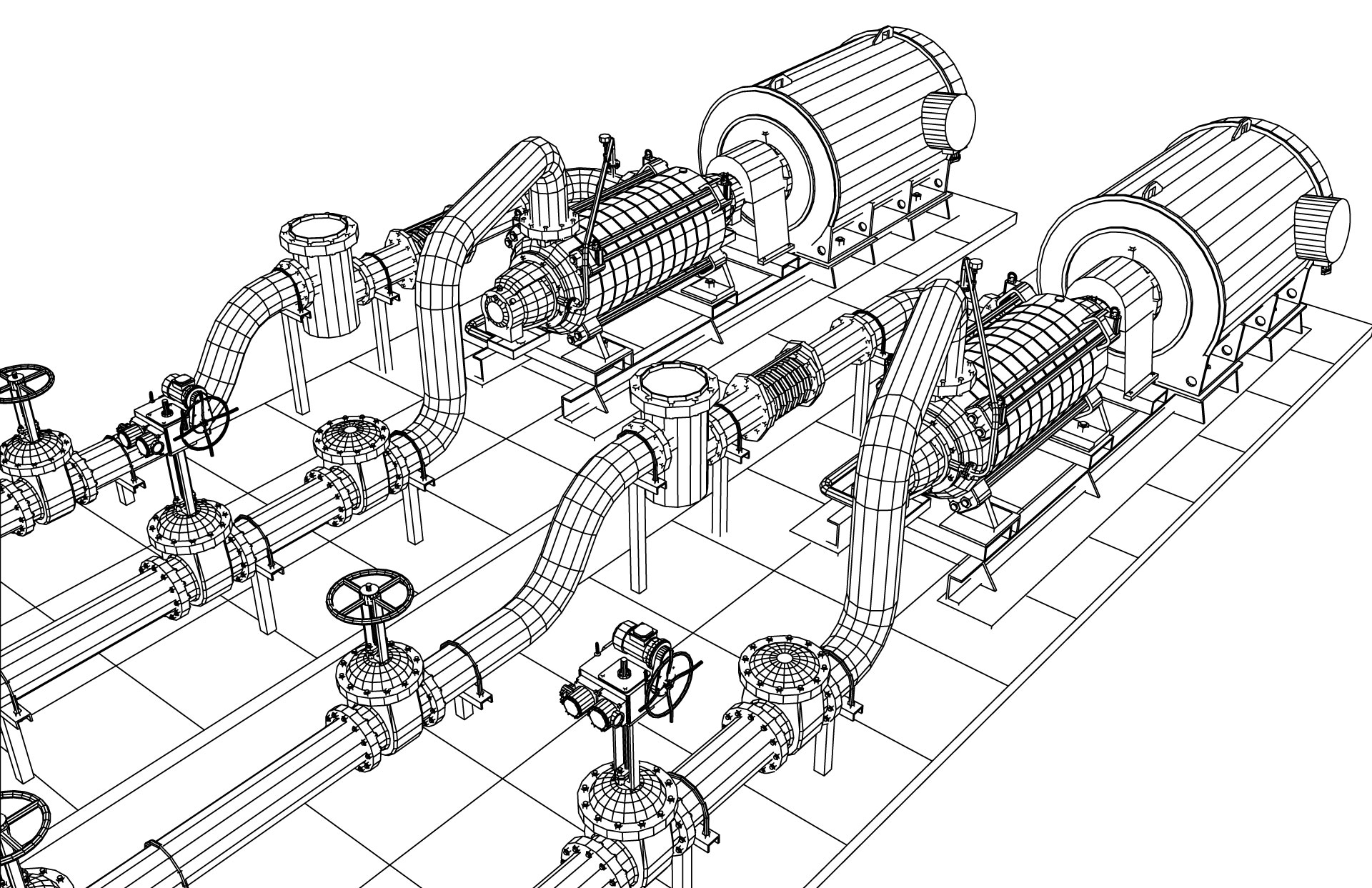
With the retrofitting technique, Service Pumps Solutions offers not only the option to modernize the performance of pump units and systems, but also improve upon their original ‘stock’ version. Through retrofitting, it is possible to add new devices, automation systems, advanced materials and more reliable components to obtain greater functionality and improved performance.
REVERSE ENGINEERING

Service Pumps Solutions offers, among its main services, Reverse Engineering. It consists of the swift analysis of an object of any shape and material, in order to reproduce a new component of similar functionality or technological improvement – in this case also increasing its efficiency. This technique is often used when the obsolete component exhibits damage or wear, even up to 80%, or when it is no longer possible to find the original spare part on the market or due to very long lead-in times.
The Reverse Engineering techniques adopted for the production of non-OEM spare parts include:
- Optical digitization systems
- Analogue and digital measuring instruments
- Chemical and structural analysis - FEM modeling finite element simulation
- Project and drawing implementation
Technologies and supplies to support Reverse Engineering include:
- ‘Lost’ plug and mould production techniques
- Semi-finished products by foundry casting or by forging
- Semi-finished products for trade
- NDT (non-destructive testing)
- Thermal treatments
- Products finished by mechanical processes incorporating interrupted or continuous machining – manual or CNC
- Surface coatings
- Static and dynamic balancing
ADDITIVE MANUFACTURING
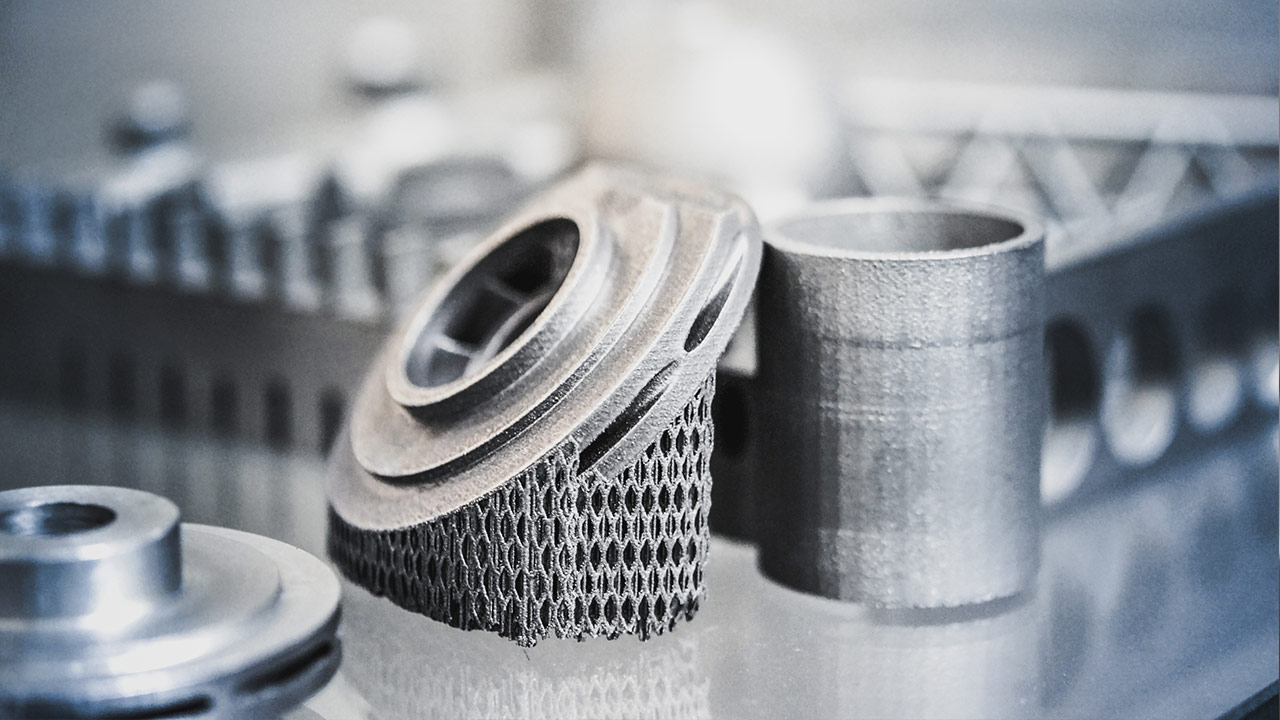
In addition to the common methods of producing non-OEM spare parts, according to particular needs and following an accurate feasibility study of the component to be replicated, Service Pumps Solutions can supply components produced by the Additive Manufacturing technique. Additive Manufacturing is a technique that can be used to build very complex components and of different types of material from polymers to metals. The additive process starts with a digital 3D model converted into a usable format for processing. The base material is deposited, and then progressively built up layer by layer similar to a common printer.
Why use additive manufacturing?
Sometimes, the necessary component is not available when needed, or is out of production and therefore no longer available. In these cases, or to improve the design, additive manufacturing can also represent the opportunity to recreate the same component to offer greater efficiency and reliability. Components can be made using original construction drawings or a design obtained with the help of Reverse Engineering. Additive manufacturing is more convenient for small production runs and rapid prototyping, where the process helps to contain economic expenditure.
In particular, after being made, the item can undergo other treatments and processes if necessary, including: thermal or chemical treatments, finishing processes using machines for de-burring, turning and milling, etc.
Advantages for the Client:
- Reproduce a geometrically complex replacement improved from the topological point of view
- Short lead times for small quantities and complex shapes
- Partial reconstruction of one or more components forming part of a single more complex unit
SUPPLY OF SPARE PARTS
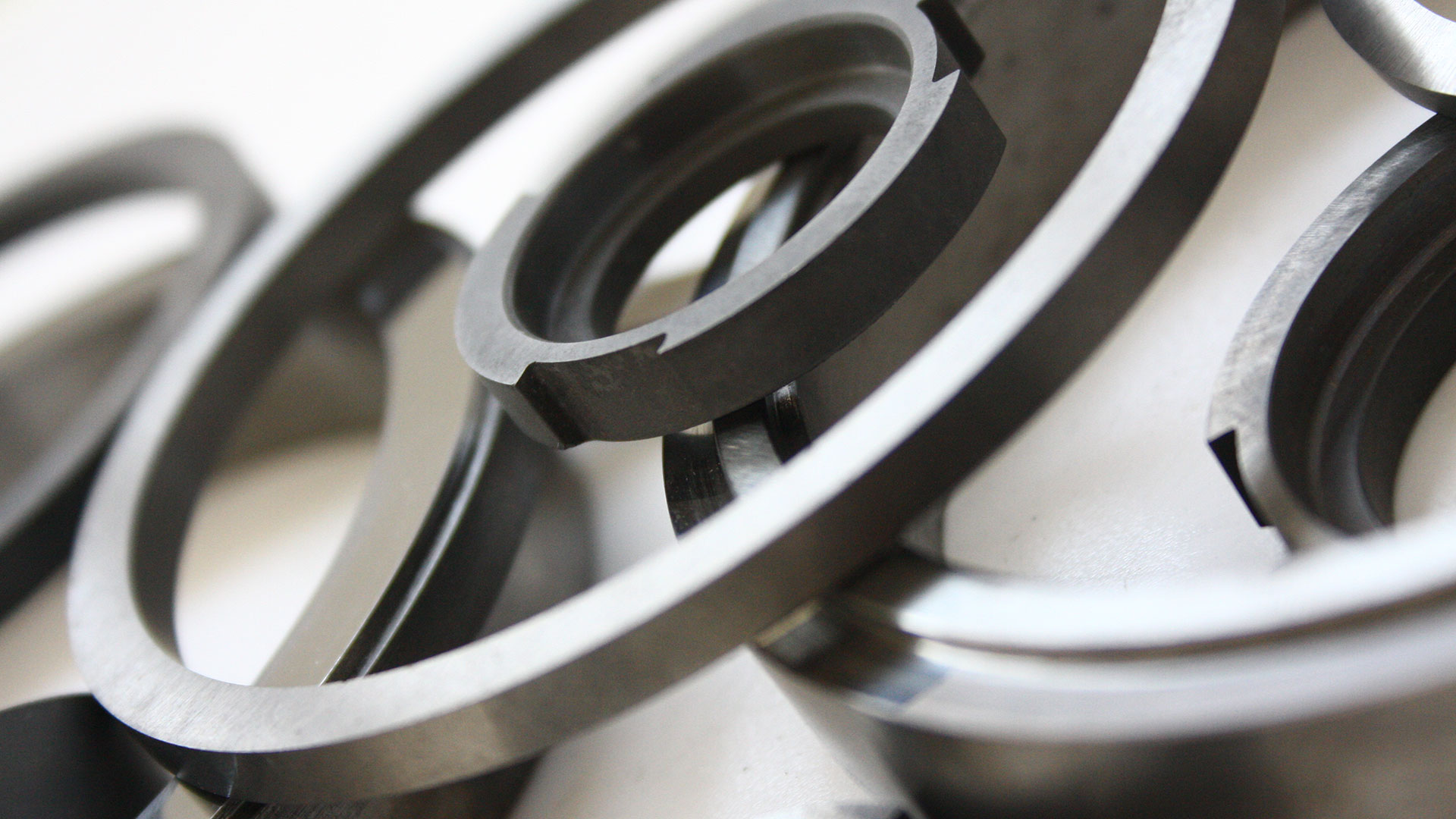
For all types of pumps, valves, rotating machines and auxiliary systems, Service Pumps Solutions can supply original and non-OEM spare parts or new complete motor / pump skids of any brand.
Verification of the integrity of an original spare part:
In the event that the original spare part has, for example, a manufacturing defect or damage due to transport, Service Pumps Solution will, upon its receipt, check its integrity, visual status, data label and any associated documentation.
Non OEM Parts:
Service Pumps Solutions performs checks on receipt of all standard and non-OEM spare parts available on the market, verifying their integrity and documentation. The highest quality is guaranteed on non-OEM spare parts directly built by Service Pumps Solutions, maintaining the same characteristics of the original spare part or even improving the technology when required or necessary. The component is followed throughout the manufacturing cycle, from the design phase, passing through the semi-finished product to the finished part. Accompanying the non-OEM spare part, all necessary documentation and certification of the material, non-destructive and destructive tests, heat treatments, coatings, etc. is issued to the customer.
DEPOSIT ACCOUNT
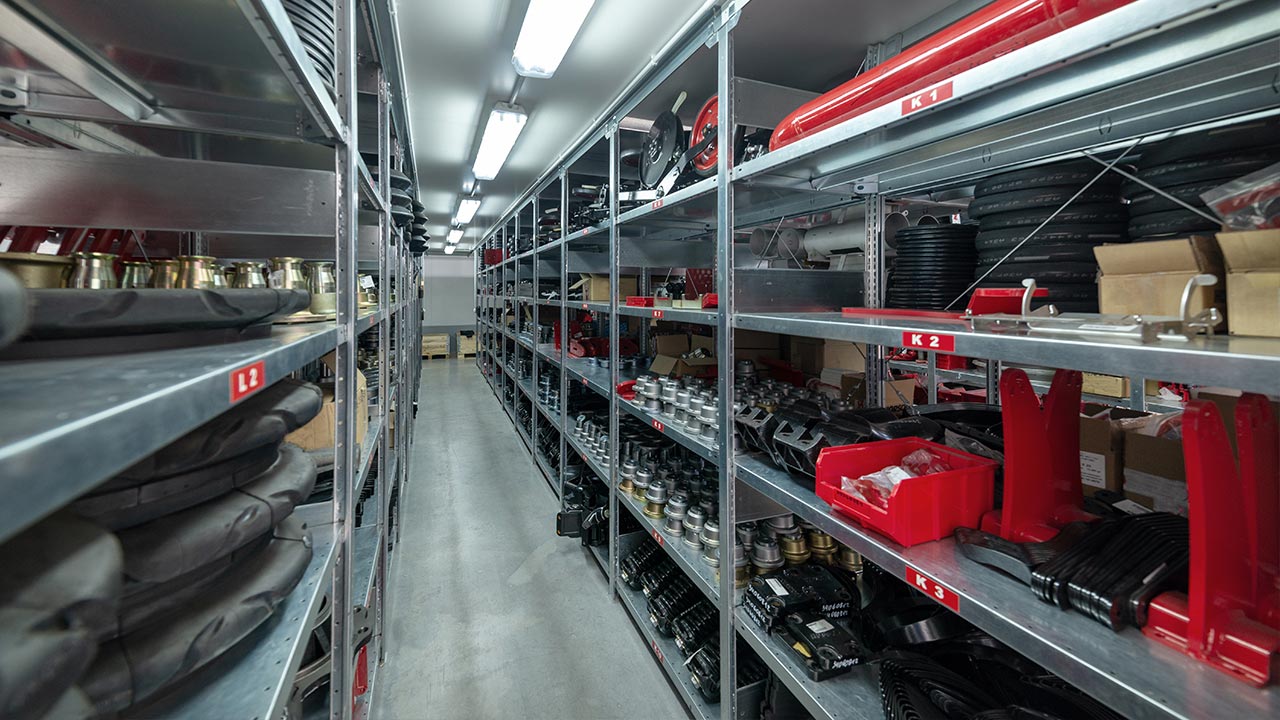
To meet the different needs of customers, Service Pumps Solutions, also offers a deposit account service. The Customer is offered the option of deposit and storage of important spare parts, pump units, pumps, motors, at the Service Pumps Solutions warehouse.
How it is managed:
- Stipulation of the deposit account contract: temporary, annual, multi-year, personalized
- Insurance Policy
- Creation of a Deposit Account Register
- Preservation of assets according to specifications
- Logistics management
Advantages for the Client:
- Reduction / elimination of own warehouse costs
- Certainty that the asset is preserved and maintained in efficiency according to specifications
- Logistics management entrusted to the supplier
- After verification and any maintenance planning, you are able to strategically choose the spare part to keep ready for use
- Stock optimization